耐磨陶瓷涂层
更新:2017-1-7 5:48:38 点击:
- 产品品牌 抗耐牌
- 产品型号 KN-17
- 产品描述
耐磨陶瓷涂层用于表面预保护高硬度陶瓷涂层,陶瓷涂层材质:氧化铬陶瓷涂层、氧化铝陶瓷涂层、氧化锆陶瓷涂层等。...
产品介绍
随着高新技术的不断发展,工程机械、设备及构件的工作条件变得日益苛刻,如水轮叶片,水电站闸门以及造纸磨浆机的磨盘等,它们不仅工作在强的腐蚀环境中,同时又不断运动、转动,承受着不同介质的冲击与磨损。一般的抗腐蚀涂料由于所形成的涂层没有足够的机械强度与耐磨性,在受到长时间冲击与机械作用后,会很快磨损,乃至剥落而失去对基材的保护作用,因而只能应用于静态工件上 。耐磨陶瓷涂层则由于兼有良好的抗腐蚀作用与优异的机械耐磨性能,已成功地应用于上述复杂的动态工作环境中,且应用范围越来越广,发展前景相当广阔。
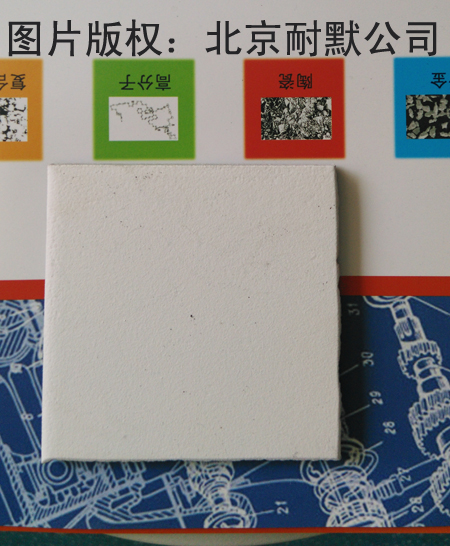
图(1)北京耐默公司喷涂制作的耐磨陶瓷涂层样板块
1 耐磨陶瓷涂层用原材料及涂层的制备方法
从化学组成上,工程陶瓷可分为氧化物陶瓷与非氧化物陶瓷两类。氧化铝、氧化钛、氧化锆及其复合物是应用广泛的氧化物陶瓷材料,也是制备陶瓷涂层的主要原料。一些高硬度的非氧化物陶瓷,如碳化硅、氮化硼、碳化钛等,也常用作耐磨涂层材料。
可制备耐磨陶瓷涂层的方法有热喷涂、物理气相沉积(PVD) 、化学气相沉积(CVD) 、溶胶- 凝胶法(Sol- Gel) 等方法,应用较多的方法是激光熔覆、等离子喷涂、物理气相沉积及胶粘陶瓷涂层法。
1.1 激光熔覆
激光熔覆又称激光涂覆或激光熔敷,其实质是将具有特殊性能(如耐磨、耐蚀、抗氧化等) 的粉末先喷涂在金属表面上或同激光束同步送粉,然后使其在激光束作用下迅速熔化、扩展及快速凝固,在基材表面上形成无裂纹、无气孔的冶金结合层的一种表面改性技术。激光熔覆具有许多优点:应用灵活、耗能小、热输入量低、引起的热变形较小,不需要后续加工或加工量很小,减少公害等。
激光熔覆陶瓷涂层技术虽然是80 年代末刚刚兴起的,但它被视为最有价值的表面强化方法而深受广大学者的重视。近年来结合原位反应技术兴起的激光熔覆自生陶瓷涂层为激光熔覆陶瓷涂层又注入新的活力,使之表现出更强劲的发展势头。
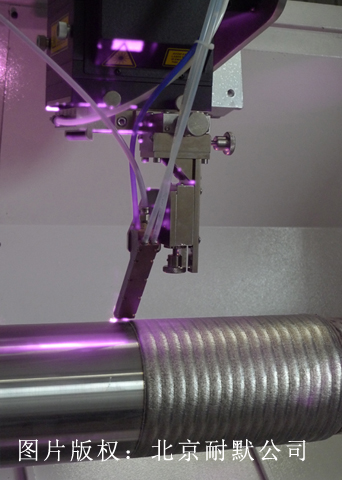
图(2)激光熔覆耐磨涂层中
耐磨陶瓷涂层是激光熔覆陶瓷涂层中研究得最早,也是最多的一种功能涂层。国内外许多研究者在不同基材上进行激光熔覆陶瓷涂层都取得了良好的耐磨效果。Ayars在铝合金表面溅射熔覆TiC 颗粒后,发现涂层在干砂磨粒磨损条件下耐磨性比末处理的铝合金提高7~38 倍。Cooper 在Inconel625 合金上采用同步送粉法激光熔覆WC、TiC 复合涂层,发现涂层的摩擦系数μk 明显低于末处理材料。李刚等人在对激光熔覆涂层与热喷涂涂层组织性能比中指出,激光熔覆涂层的硬度、耐磨性较热喷涂涂层有较大提高,激光熔覆层最高硬度达到HK900 ,而热喷涂层最高硬度为HK700。
激光熔覆陶瓷涂层也存在一些不足之处。由于在激光熔覆过程中,熔覆层被快速加热、熔化,然后又急剧冷却,属非平衡凝固,而且涂层材料和基体材料差异较大,再加上激光处理过程中影响因素较多,致使熔覆层质量不易控制,结果常在涂层中出现某些缺陷,如气孔、裂纹、烧损等。
1. 2 等离子喷涂
等离子喷涂是热喷涂中的一种,指利用等离子弧将各种金属、合金以及陶瓷、塑料等熔化后高速喷射到工件表面上,从而与基体形成一层牢固的涂层,达到高度耐磨、减摩、耐蚀等目的。等离子喷涂陶瓷涂层技术可提高零部件的耐磨性和耐蚀性,在机械和航空等领域中已获得较广泛的应用。喷涂材料一般选用Al2O3 、Cr2O3 、TiO2 等陶瓷粉末。等离子喷涂分为大气等离子(APS) 、超音速等离子喷涂(HVPS) ,真空等离子喷涂(VPS) 等,APS 适应性强,可通过控制工艺参数制备精细涂层。其主要缺陷是涂层与基体以机械结合为主,结合强度低,难以适应冲击、高应力、强疲劳等工作条件。超音速等离子喷涂具有更高的功率和温度,更适应喷涂陶瓷。近几年广泛应用的VPS 制备的涂层更为致密,结合强度也更高。等离子喷涂技术具有许多优点:
(1) 等离子喷涂时的焰流温度高,热量集中,能熔化一切高熔点和高硬度的粉末材料;
(2) 由于等离子喷涂时的焰流喷射速度高,粉末微粒能获得较大的动能,所以喷涂后的涂层致密度高;
(3) 喷涂后涂层平整、光滑,并可精确控制涂层厚度;
(4) 喷涂工艺规范稳定,调节性能好,容易操作。
其缺点是:喷涂作业环境差,粉尘污染严重,喷涂材料利用率低等。
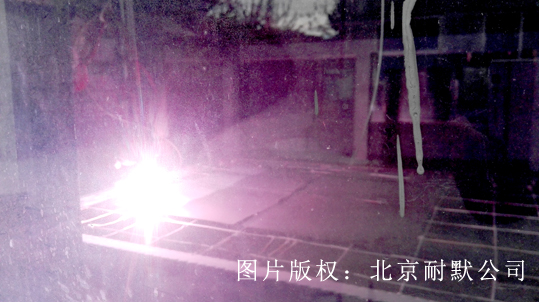
图(3)等离子喷涂陶瓷涂层
任靖日等人研究了AC4C 铸铝合金表面等离子喷涂Al2O3 - 40 % TiO2 和Cr2O3 陶瓷粉末涂层的滑动摩擦磨损特性,指出在相同条件下硬度较高的Cr2O3涂层的耐磨性高于Al2O3240 %TiO2 。陈传忠等人所研究的Al2O3 + TiO2PNiCrAlY复合陶瓷涂层,由于熔化的TiO2 和Al2O3 形成了一定程度的互熔,进一步提高了涂层的硬度和耐磨性能。
1. 3 物理气相沉积法(PVD)
PVD 法又分为溅射法、离子镀法和蒸镀法。离子镀法是用离子束使蒸发源的材料蒸发变成原子,并被在基体周围的等离子体离子化后,在电场作用下以更大动能飞向基体形成涂层。这种涂层均匀致密,与基体材料结合良好。溅射法即以动量传递的方法将材料激发为气体原子,并飞出溅射到对面的基体上,沉积而形成涂层。蒸镀法即蒸发镀膜,是用电子束蒸发源的材料蒸发成离子(原子或离子) 而沉积在工件上形成涂层。
离子镀可以使氧气和金属蒸气反应生成ZrO2 、AlO3 、Cr2O3 、TiO2 的陶瓷涂层,再利用蒸镀与离子束(EB) 技术结合产生的EB - PVD (离子束物理气相沉积) 技术制备的陶瓷涂层,耐磨性及使用寿命要比等离子喷涂涂层提高一个数量级。
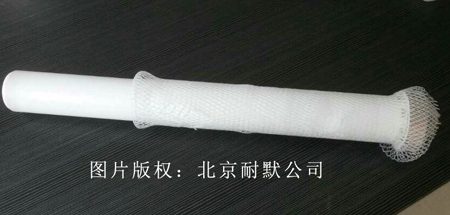
图(4)耐磨陶瓷涂层用于活塞杆
1. 4 耐磨胶粘涂层制备法
耐磨胶粘涂层制备法是指将胶粘剂基料和硬质耐磨材料或减摩材料按适当比例和规范混合起来,涂敷于清理好的零件表面,以获得所需性能涂层的一种表面技术。一般说来,耐磨胶粘涂层的涂料由粘料、固化剂、特殊填料及辅助材料四部分组成。
粘料又称为粘接剂,可分为有机粘接剂和无机粘接剂两大类。有机粘接剂一般指合成树脂,不同的树脂由于其不同的组成与结构,而使所构成涂料的耐磨性有所不同,如表1 所示。
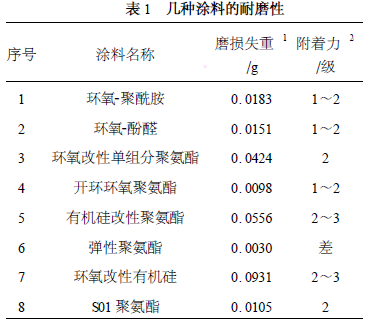
1 磨损失重:按GB - 17690 - 79 进行,测定负荷为500g ,转数为500r 条件下测定的结果。
2 附着力按GB - 1720 - 79 进行,画圈法。
从表1 可以看出,耐磨涂料所用树脂主要分为三类,即环氧树脂类,聚氨酯树脂类、有机硅树脂类及各自的改性物。其中聚氨酯类特别是弹性聚氨酯的耐磨性最好 。
弹性聚氨酯( PU) 具有两相结构的特点,连续相(软段) 为聚酯或聚醚链段,非连续相是由二异氰酸酯和二元醇反应制得的刚性链段。由于其特殊的软硬两相结构,不仅能最大限度地吸收来自外部介质的冲击作用,而且同时维持自身足够的刚度与机械强度,因而耐磨性优异。但是,弹性聚氨酯对金属底材的附着力较差,不能直接用于涂料。
图(5)耐磨胶粘涂层,型号 KN17,北京耐默公司用于各种设备预保护
环氧树脂(EP) 具有良好的附着力,且固化后涂料具有较高强度,因此环氧耐磨涂层得到大量研究。潘国顺等人用环氧树脂和90 目氧化铝制备的耐磨涂层具有较好的耐浆体冲蚀、磨蚀性能。以45 号钢为参考试样,其相对耐磨性达到8. 2。马向东等人研制的环氧耐磨胶的耐磨性能也明显优于高铬铸铁和20号钢。
虽然环氧树脂具有优良的粘接力和机械强度,但缺乏韧性,往往呈脆性状态,改善环氧树脂基体的韧性是提高涂层耐磨性的有效途径。人们曾尝试采用聚硫橡胶、丁腈橡胶、氯丁橡胶、尼龙等来改性环氧树脂。以短羟基丁腈橡胶对环氧树脂进行增韧的研究最多,增韧效果也较好,在工业上得到广泛应用。聚氨酯树脂具有极佳的柔韧性和弹性,人们早在上世纪60 年代末就开始用其对环氧树脂改性。美国Dow Chemical 公司首先研制成功聚氨脂改性环氧结构胶粘剂,复合材料基体树脂等产品,并用于航空航天工业 。国内的有关研究也不少,上海市合成树脂研究所在DW - 4耐超低温胶中,用了环氧改性的聚氨酯树脂。黑龙江省石油化学研究所研制出聚氨酯半互穿改性环氧树脂胶粘剂,增强了它的剪切强度和剥离强度。李莉等人用聚氨酯对环氧树脂改性,不仅提高了粘合剂的粘接性能,还提高了力学性能,增强了韧性。高义民等人采用李莉等人研制的改性环氧树脂为基体,以Al2O3 颗粒为增强相,制备的胶粘涂层抗冲蚀磨损特性为正火态45 号铸钢的36 倍。美国弗利康公司开发的Owens -Coming 耐磨涂料选用双酚A 型环氧树脂和聚氨酯弹性体为胶粘剂,经检测为性能优异的耐磨涂料。
要求防腐耐磨的高温涂料多采用经环氧树脂改性的有机硅树脂,纯有机硅树脂制备的耐磨涂料的耐磨性相对较差。黄志等人研制的耐温耐磨有机硅涂料的冲蚀率比一般的金属高一个数量级以上。
图(6)耐磨胶粘涂层现场施工中
耐磨涂料所选用的无机结合剂主要有硅酸盐、磷酸盐和硼酸盐三类。无机涂料由于污染小,且耐高温和耐磨性能优于有机结合剂,故近年来得到了较快发展。罗立新等人用研制的无机高温耐磨粘涂剂,制成的涂层耐磨性为2OG钢的10 倍多。然而,无机涂料是水溶性涂料,耐水和耐冲蚀性能都有待提高。陈秀琴等人综述了目前提高硅酸盐无机高分子涂料耐水性能的几种有效途径。
填料是耐磨胶粘涂层至关重要的另一组成部分。耐磨填料一般包括一种或多种高硬度磨料如刚玉、金刚砂、金属氧化物等。此外还需加入一些减摩材料如石墨、二硫化钼、聚四氟乙烯等。随着纳米技术的开发与应用,纳米粒子的加入将有助于耐磨涂料的力学性能提高。目前主要研究纳米CaCO3 、iO2 、滑石粉、硅酸铝、铁系颜料等对涂膜耐擦洗、耐磨、附着力、抗冲击、柔韧性的改进。纳米SiO2 添加到紫外光固化涂料中可提高涂料的硬度和附着力, 如表2所示。纳米CaCO3 可提高聚氨酯的强度、硬度等;各向异性分散的纳米层状硅酸盐可提高酸酐固化的环氧树脂的韧性。
表2 纳米SiO2 对涂膜硬度的影响
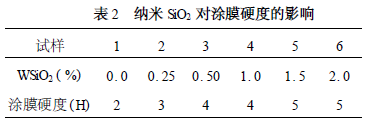
1.5 其它几种耐磨涂层的制备方法
耐磨涂层的制备方法还包括化学气相沉积法、溶胶- 凝胶法、自蔓延高温合成法(SHS) 等。
化学气相沉积法是指在相当高的温度下,工作气体与基体的表面相互作用,使其中的某些成分分解,并在基体表面形成一种金属或化合物的固态膜或镀层。该法制备的涂层均匀,组织细微致密、纯度高,与基体结合牢固,但制备速度慢,涂层较薄。溶胶- 凝胶法是以易水解的金属醇盐或无机盐在某种溶剂中与水发生反应,经水解缩聚形成溶胶,并将溶胶涂覆在金属表面上,再经干燥、热处理后形成涂层。此方法制备的涂层均匀性高,反应可在较低温度下进行,所需设备简单,操作方便,但涂层通常较薄,防腐和耐磨性能均不理想。自蔓延高温合成法是指充分利用化学反应所释放出来的能量使生成物处于熔融状态,由于离心力的作用,在金属管内形成陶瓷涂层。该项技术的优点是,能耗低、效益高;陶瓷层厚大于2mm ,具有优异的耐磨损性能和耐热性能;涂层与钢管内壁界面结合强度高,不易剥落和损坏。缺点在于制备涂层的工艺过程较难控制,目前无法在工业中推广使用。
2 结语
随着科技进一步发展,耐磨陶瓷涂层将会得到更广泛的应用。在众多陶瓷涂层的制备技术中,胶粘陶瓷涂层因制造工艺简便,易于施工,成本低廉等优点得到迅速发展。目前所使用的耐磨胶粘涂料大多为溶剂型涂料,具有一定的污染和毒害性。今后,耐磨胶粘涂料将向环保型涂料如高固体份、粉末和水性涂料方面发展,并开发性能更加完备、使用更简便的改性树脂以及利用高新技术制备高性能的惰性耐磨填料,发展新的涂层工艺。同时,加强对耐磨涂层的腐蚀、磨损性能的微观机理研究,为以后具体的开发工作提供明确的理论基础。
更多产品